2. Inventory Check: Before shipping, staff will check the inventory to ensure that the required products are in stock and ready for shipment.
3. Packaging: Strollers need to be properly packed to ensure they are not damaged during transportation. Durable packaging materials are usually used and relevant labels and barcodes are affixed to the packaging.
4. Inspection and quality control: Before leaving the warehouse, products usually undergo final inspection and quality control to ensure compliance with the company's quality standards and certification requirements, such as EN1888, ASTM and 3C standards. This may involve visual inspections, functional tests, safety checks, etc.
5. Identification and records: Put identifiers such as logos, barcodes or serial numbers on the product packaging, and record the product's outbound information, such as outbound date, quantity, etc.
6. Shipping: After the outbound process is completed, the product will be ready for shipping. The appropriate logistics partner or shipping method is often used to ensure that the product reaches the customer safely.
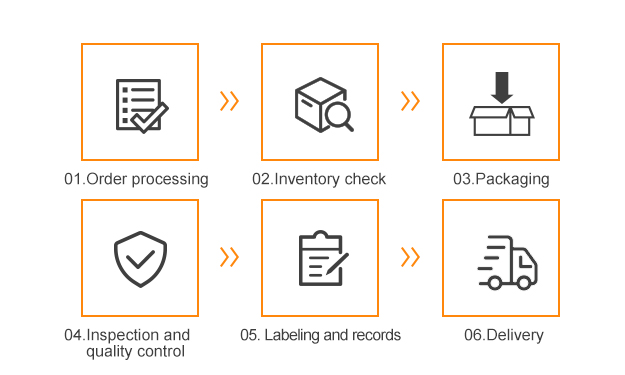